اتصل
هاتف
+0086-371-86162511
عنوان
تشنغتشو ، الصين
coal grinding specific power mill

(PDF) MPS mills for coal grinding ResearchGate
PDF Two mill systems are employed for most coal grinding applications in the cement industry. These are, on the one hand, vertical roller mills (VRM) Find, read and cite all the researchAbstract. In this study, experimental data for wet- and dry-ground coal samples under wet and dry grinding are characterized by commonly used distribution Wet and dry grinding of coal in a laboratory-scale ball
احصل على السعر
Modelling SAG milling power and specific energy
The relative specific energy efficiency can be considered as the relative amount of energy for various grinding conditions. The variation between relative energy The problem of minimizing the specific energy consumption for grinding and transporting Azean coal in an ShK-32 ball drum mill is considered. For moist brown Determining Optimum Productivity of a Ball Drum Mill
احصل على السعر
(PDF) Practical assessment of grinding capacity and power
PDF This paper analyzes the effects of coal grindability and its characteristics on the grinding capacity and power consumption for beater wheel mill Coal Grinding. To achieve good combustion and satisfactory flame formation, coal needs to be dried and ground to a proper degree of dryness and fineness. Drying of moisture in coal is achieved normally by ducting part of the kiln exhaust gas through the mill with inlet temperatures of up to 300°C. Inert kiln exhaust gases with oxygen contentCoal Grinding Cement Plant Optimization
احصل على السعر
MPS mills for coal grinding AYS Engineering
2 Design features of MPS mills for coal grinding. Depending on the material to be ground, throughput rates of 5-200 t/h can be achieved in a fineness range between 1% R0.063 mm and 25% R0.090 mm. Thus, the MPS coal grinding mill device for fresh material is arranged in this area where the fresh feed is also mixed with the grits A compact coal mill solution for grinding virtually any type of raw coal. Our ATOX® Coal Mill is a compact vertical roller mill that can grind almost any type of raw coal. The coal mill utilises compression and shear force generated between the large rollers and the rotating table to crush and grind raw coal, removing the need for a separateATOX® Coal Mill FLSmidth
احصل على السعر
What is a Coal Grinding Mill ball mills supplier
When choosing a coal grinding mill, it is important to consider several factors, including the specific application, grinding requirements, and capacity. Factors to consider include the type of material being ground, the desired particle size, the moisture content of the material, and the required grinding capacity.A particle size reduction model has been developed as the first component of an upgraded ball mill model. The model is based on a specific energy-size reduction function, which calculates the particle breakage index, t 10, according to the size-specific energy, and then calculates the full product size distribution using the t 10 –t n A specific energy-based size reduction model for batch grinding
احصل على السعر
Review on vertical roller mill in cement industry & its performance
Vertical Roller Mills (VRM), High Pressure Grinding Rolls (HPGR), Vertical Shaft Impact Crushers (VSI) and more recently, Horizontal Roller Mill (Horomill) have saved the specific power by 45–70% when compared with a ball mill circuit [8], [10]. Now a days Ball mills and HPGR are installed together as a common unit.Batch stirred ball mill grinding results demonstrate that this new technique has a great potential in reducing the energy consumption of fine coal grinding. Depending more » on the pretreatment conditions, the specific energy consumption of producing less than 10 {mu}m product is reduced to 41-60% of that of the untreated coal Field-scale investigation of pulverized coal mill power
احصل على السعر
Reprint from ZKG 3 Gebr. Pfeiffer
coal grinding applications in the cement industry, where normally a two-mill-system is used. 1 Introduction Two mill systems are employed for most coal grinding applications in the cement industry. These are, on the one hand, vertical roller mills (VRM) that have achieved a share of almost 90 % and, on the other hand, ball mills whose share de -It pulverizes coal by applying hydraulically-loaded grinding pressure through three grin- ding rollers onto a rotating bed of coal. Grinding pressure can be adjusted to account for variations in coal grindability and desired product fineness. Raw coal is fed through a centrally located feed pipe to the center of the grinding table.A Comparison of Three Types of Coal Pulverizers Babcock Power
احصل على السعر
Modeling of Coal Mill System Used for Fault Simulation MDPI
The medium-speed coal mill system is mainly composed of raw coal bunker, coal feeder, coal mill, primary fan, sealing fan, hot and cold air regulating valves. The coal feeder transports the raw coal from bunker to mill for grinding. The primary air is divided into two paths after being pressurized by primary fans.Introduction. Replacing some of the coal by biomass is an effective way to reduce CO 2 emissions from pulverized-coal-fired power plants and integrated coal gasification-combined cycle power plants. However, compared with coal, biomass has lower grindability in the existing roller mills 1 and a lower calorific value per weight. 2,3 Milling Characteristics of Coal and Torrefied Biomass Blends in a
احصل على السعر
P N ALL D LL AT THAL Neliti
of the grinding facilit ewords drum ball mill, coal grinding, efficienc improvement, thermal power plant, regression analsis C 21 10.155/1201.2022.250 How to Cite: Kamarova, S., Abildinova, S., Terziev, A., Baidyussenov, G. (2022). Improving th efficiency o th coa grinding proces in bal drum mill at therma powe plants.Coal Grinding Capacity kg/s 25. Mill Speed rpm 28. Diameter of Roller mm 1880. Table Diameter mm 3625. The specific material resilient to abrasion is required to extend operating services.An investigation of performance characteristics and
احصل على السعر
A specific energy-based size reduction model for batch grinding
A particle size reduction model has been developed as the first component of an upgraded ball mill model. The model is based on a specific energy-size reduction function, which calculates theY. Reichardt. G. Link. H. Gilabert. Since the beginning of 2002, Industrias Rocacem S.A has been operating an MPS 4250 BC roller mill at their Latacunga grinding plant in Ecuador. The mill(PDF) MPS mills for coal grinding ResearchGate
احصل على السعر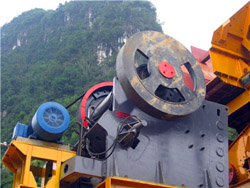
Quantifying the energy efficiency of fine grinding circuits
Size Specific Energy (SSE) differs by relating the grinding energy to the quantity of new fines generated. For typical circuits that involve AG/SAG, HPGR or ball milling, the generation of -75 µm material (denoted as SSE75) is a suitable marker size with which to benchmark performance because it contains 80% of the surface area About 2% of the electricity produced in the whole world is used during the grinding process of raw materials [1]. While total electrical energy consumption for cement production is about 100 kWh/ton of cement, roughly two thirds are used for particle size reduction [2]. About 65% of the total electrical energy used in a cement plant is utilizedReducing energy consumption of a raw mill in cement industry
احصل على السعر
COAL PULVERIZER DESIGN UPGRADES TO MEET THE DEMANDS
grinding rollers fixed to the loading frame are thus pressed against the coal bed between the rollers and grinding table segments (Figure 4).The applied grinding load is capable of being adjusted in real time with the mill in operation. Figure 4. Hydropneumatic grinding force loading system.The 30 mm ball draws slightly more power as J increases from 11 to 16% but the gain in capacity is much more. In fact for an increase in J from 11 to 16% (i.e. 45% increase), power draw increase is 31%, while capacity increases by 51%. For the 50 mm balls the respective increase in power and capacity is 28% and 42%.Exploring ball size distribution in coal grinding mills
احصل على السعر
Optimization of operating conditions on ultra-fine coal grinding
This study investigated ultra-fine coal grinding performance of four low- to moderate-cost grinding media in a laboratory stirred mill. Kinetic grinding tests showed that silica beads generated the finest product size with a P 80 of 5.9 μm from a feed size of 24.4 μm while having a specific energy (SE) input of 309 kWh/ton. Nonetheless, the
احصل على السعر- الصين طاحونة تعليق الضغط العالي
- كيفية جعل طاحونة لطين
- cheap screen doors cavite
- معدات ثقيلة السيريال 26018
- مطحنة ريموند الألمانية للبيع
- آلة طاحونة والسعر في الهند
- pulverizer machine for incense stick manufacturing
- نموذجية مشاكل طاحونة الخام العمودية
- طاحونة حبة الأفقية في عملية رسم خط
- مسبك سعر خط إنتاج الرمل
- Jaw Crusher Chrome Ore
- موردو آلات تصنيع الرمل الصناعي في الجزائر
- معدات استخراج خام الذهب بمحرك خام
- سحق مطرقة الطوب
- what is it iron ore thickening process