اتصل
هاتف
+0086-371-86162511
عنوان
تشنغتشو ، الصين
resulting product is a grinding process
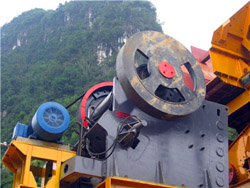
Grinding (abrasive cutting)
Selecting which of the following grinding operations to be used is determined by the size, shape, features and the desired production rate. Creep-feed grinding (CFG) was a grinding process which was invented in Germany in the late 1950s by Edmund and Gerhard Lang. Normal grinding is used primarily to finish surfaces. But CFG is used for high rates of material reGrinding is a manufacturing process that belongs to the group of material removal processes. Material removal processes where a chip is formed can be Grinding SpringerLink
احصل على السعر
Effect of different parameters on grinding efficiency and
The systematic consideration of a grinding process requires the knowledge of inputs and outputs of the grinding process. In fact, a grinding process is a material removal Grinding processes are very complex due to the multitude of influencing parameters, resulting from the stochastic tool topography with numerous Potentials of grinding process simulations for the analysis of
احصل على السعر
Efficiency and effectivity of high precision grinding
[12] defines the aim of a grinding process to obtain the finished product with minimum production cost, maximum production rate and the finest possible surface Grinding is a manufacturing process which significantly contributes in producing high precision and durable components required in numerous applications such as aerospace, defence and...(PDF) A comprehensive review on the grinding process:
احصل على السعر
Grinding SpringerLink
Some studies have pointed to the effect of grinding aids on various factors such as energy consumption, agglomeration, product coating on grinding media, The success of the manufacturing process which involves grinding as one of the stages depends solely on the accuracy of the grinding process. Being the last Development of Real-time Grinding Process Monitoring
احصل على السعر
High-performance grinding—A review ScienceDirect
High-performance grinding is essential to achieve high dimensional accuracy and surface integrity of ground components at optimum cost efficiency. The The grinding process, which turns the solid cocoa nibs into a liquid cocoa liquor, plays a significant role in shaping the ultimate chocolate experience. It intensifies the cocoa’s taste, releases the coveted cocoa butter, and ensures the resulting chocolate possesses a smooth, melt-in-your-mouth quality that we all adore.What is Cocoa Grinding? Whitakers Chocolates Our Blog
احصل على السعر
Micromachines Free Full-Text Investigating the Effect of Grinding
High-speed rail grinding is a unique passive grinding maintenance strategy that differs from conventional grinding techniques. Its grinding behavior is dependent on the relative motion between the grinding wheel and rail; hence, it possesses great speed and efficiency. In this study, the effects of the duration of grinding time and has become of great practical interest in the field of grinding grain. It is possible to significantly reduce the specific energy consumption for the production of concentrated feed and obtain a product with a high uniformity of particle size by combining the grinding process with shearing and chipping [5,8–15].Studies of a Rotary–Centrifugal Grain Grinder Using a
احصل على السعر
Minerals Free Full-Text Research on Grinding Characteristics
The particle size composition of grinding products will significantly affect the technical and economic indexes of subsequent separation operations. The polymetallic complex ores from Tongkeng and Gaofeng are selected as the research object in this paper. Through the JK drop-weight test, the batch grinding test, and the population-balance Cryogenic grinding is a process of grinding materials at shallow temperatures, typically below −150°C. resulting in a more consistent product that can be used in various recipes.Cryogenic Grinding: A Revolutionary Process in the Food Industry
احصل على السعر
Sustainability Free Full-Text Studies of a Rotary–Centrifugal
A scientific and technical literature review on machines designed to grind fodder grain revealed that the existing designs of grinding machines—those based on destruction by impact, cutting, or chipping—have various drawbacks. Some disadvantages include high metal and energy intensity, an uneven particle size distribution of the ground Results revealed that a method of grinding used in the milling process had a significant ( P < 0.05) effect on the properties of GRF and the resulting sweet dumplings. Dry milling (low temperature impact milling and roller milling) resulted in higher damaged starch content and coarser particle size than wet milling.Effects of milling methods on the properties of glutinous rice flour
احصل على السعر
Energy-Efficient Advanced Ultrafine Grinding of Particles Using
The present literature review explores the energy-efficient ultrafine grinding of particles using stirred mills. The review provides an overview of the different techniques for size reduction and the impact of energy requirements on the choice of stirred mills. It also discusses the factors, including the design, operating parameters, and feed process through a reduction of grinding time for a specific gear grinding machine. Therefore, the product quality resulting from grinding parameters contributing to an improved grinding time will be investigated. The goal was to analyse the product quality with the motivation to identify interplays andGenerating gear grinding
احصل على السعر
What Is Grinding and Its Working Principle and Type?
Grinding process is a micro-processing method. plastic molds, and automobile panel molds that require high product appearance quality are widely used. What Is the Working Principle of the abrasive and the processed surface of the workpiece have a chemical effect during the grinding process, resulting in a very thin oxideGrinding is a staple size-reduction process to produce food powders in which the powdered form is chemically and microbiologically stable and convenient to use as end products or intermediate products. The moisture content of food materials before grinding is a particularly important factor, since it determines the materials’ physical Effect of Moisture Content on the Grinding Process and Powder
احصل على السعر
Potentials of grinding process simulations for the analysis of
Grinding processes are very complex due to the multitude of influencing parameters, resulting from the stochastic tool topography with numerous geometrically undefined abrasive cutting edges. Thus, the efficient design and optimization of these processes is a challenging task. Process simulations can be used as a flexible tool for Towards the grinding process of ceramics, this operation can be classified into the lower shelf of hardness ratio between product and grinding media (Joost and Schwedes, 1996). The organic product particles have a much lower hardness compared to the grinding media, thus, they have the ability to protect grinding media Tailoring product formulation properties to reduce grinding
احصل على السعر
Material recovery and recycling of waste tyres-A review
The resulting rubber crumb is usually screened for any residual metal components before proceeding to the next step. The wet grinding process produces a product that is finer than ambient grinding. The removal of heat through water prevents the polymer chains from breaking down and produces a cleaner,Grinder. Grinding. A grinding wheel is a tool for grinding. It is composed of coarse-grained abrasive compounds bonded together. After forming a solid round object, grinding and abrasive processing can be performed on a grinding machine. Grinding is a commonly used processing method, which can obtain higher workpiece density and What is the Grinding Process and Grinding Wheel?
احصل على السعر
In-process measurement of Barkhausen noise and resulting
DOI: 10.1016/j.cirpj.2020.11.011 Corpus ID: 229463633; In-process measurement of Barkhausen noise and resulting productivity increase potential in grinding of case hardened steelGrinding is an essential process in the manufacture of virtually all types of mechanical equipment and cutting tools. For example, the production of rolling element bearings, automotive components, power generation equipment, and computer and electronic components is critically dependent on grinding processes.Grinding Processes SpringerLink
احصل على السعر
Grinding Chocolate: Processing Insights
Grinding: Transforming Nibs into Chocolate Liquor. Having successfully separated cocoa nibs from their shells, the next crucial step in chocolate processing is grinding. This process involves converting the cocoa nibs into a smooth, flowing liquid known as chocolate liquor. Let us delve deeper into this transformative stage.Grinding is mostly considered as a finishing operation by which a high surface quality is achieved. An increase in productivity is therefore limited by maintained surface properties such as the roughness or tensile residual stresses. Thus, a roughing operation is inevitable followed by a finishing operation, while both operations are Process design of a novel combination of peel grinding and deep
احصل على السعر- hello crush waste crusher
- الكسارات الخرسانية للإيجار في ولاية ماريلاند
- مستثمر يبحث عن مشروع محاجر الجبس
- مطاحن طحن مسحوق رقيق
- impact for coal crusher
- كسارة خام الحديد للبيع أوريسا
- تنقية الذهب المكثف من جنوب أفريقيا
- طاحونت البابا كيرلس
- Japan Roller Crusher 3a Prc Series
- تحويل طاحونة بريدجبورت إلى التصنيع باستخدام الحاسب الآلي
- طحن الأسمنت وسائل الإعلام التعدين فائدة advantgaes آلة
- السعودية مصنع الكرة مطحنة
- hs code crushing machine
- معدات ثقيله السودان
- غسيل الحصى في دبي