اتصل
هاتف
+0086-371-86162511
عنوان
تشنغتشو ، الصين
grinding ball mill process

(PDF) Grinding in Ball Mills: Modeling and Process
A ball mill is a type of grinder widely utilized in the process of mechanochemical catalytic degradation. It consists of one or Grinding in Ball Mills: Modeling and Process Control. Vladimir Monov, Blagoy Sokolov and. Stefan Stoenchev. Published Online: 16 Mar 2013. Volume & Issue: Grinding in Ball Mills: Modeling and Process Control Sciendo
احصل على السعر
Process engineering with planetary ball mills RSC
Processes inside planetary ball mills are complex and strongly depend on the processed material and synthesis and, thus, the optimum milling The paper presents an overview of the current methodology and practice in modeling and control of the grinding process in industrial ball mills. Basic kinetic and Grinding in Ball Mills: Modeling and Process Control
احصل على السعر
Grinding in Ball Mills: Modeling and Process Control
Materials Science 2022 7th International Conference on Mathematics 2022 The paper presents advanced technologies and equipment for metal powder Ball milling is a mechanical technique widely used to grind powders into fine particles and blend materials.18 Being an environmentally-friendly, cost-effective technique, it has found wide application in industry all over the Ball milling: a green technology for the
احصل على السعر
Intelligent optimal control system for ball mill grinding
Abstract: Operation aim of ball mill grinding process is to control grinding particle size and circulation load to ball mill into their objective limits respectively, while Ball grinding process is a grinding method of crushing ore with ball-shaped grinding medium in the grinding mill. In the ball grinding process, because the steel ball Ball Grinding Process SpringerLink
احصل على السعر
Investigating grinding mechanisms and scaling criteria in a ball mill
Grinding powders in a ball mill is a complex operation in which many parameters, such as geometrical factors [2], filling ratios [3], powder properties [4] or the The ball mill process parameters discussed in this study are ball to powder weight ratio, ball mill working capacity and ball mill speed. As Taguchi array, also known as orthogonal array design, adds a new dimension to conventional experimental design, therefore, Orthogonal array (L9) was carefully chosen for experimental design to Comparative Study on Improving the Ball Mill Process
احصل على السعر
Producing Metal Powder from Machining Chips Using Ball Milling Process
The process of ball milling involves the grinding and mixing of metal particles within a ball mill, which is a type of equipment used for grinding, with the aim of producing a fine powder . This method has been widely employed in the manufacturing of metal powders from diverse sources, including metals, alloys, and intermetallic compounds.The ball mill Ball milling is a mechanical technique widely used to grind powders into ne particles and blend materials.18 Being an environmentally-friendly, cost-effective technique, it has found wide application in industry all over the world. Since this mini-review mainly focuses on the conditions applied for the prep-Ball milling: a green technology for the preparation and
احصل على السعر
Ball mill load status identification method based on the
A ball mill is important grinding equipment in a concentrator, and the accurate detection of the load status ensures that the ball mill runs in the best state, which helps optimize the grinding process, ensure the stable operation of the ball mill equipment, and save energy. The current mainstream detection methods cannot easily detect the MA is a stochastic process that involves many process variables such as type of mill, milling container, milling energy/speed, milling time, type, size, and size distribution of grinding medium, ball-to-powder weight ratio, extent of vial filling, milling atmosphere, process control agent, and temperature of milling.Full article: Mechanical alloying: a critical review
احصل على السعر
Grinding in Ball Mills: Modeling and Process Control
An overview of the current methodology and practice in modeling and control of the grinding process in industrial ball mills is presented. Abstract The paper presents an overview of the current methodology and practice in modeling and control of the grinding process in industrial ball mills. Basic kinetic and energy models of the grinding Abstract The paper presents an overview of the current methodology and practice in modeling and control of the grinding process in industrial ball mills. Basic kinetic and energy models of the grinding process are described and the most commonlyGrinding in Ball Mills: Modeling and Process Control
احصل على السعر
Ball milling as an important pretreatment technique in
The result revealed that the energy required by a ball mill, high-pressure homogenizer and twin screw extruder were 232.5, 43.3, and 5 kWh/kg of biomass, respectively . Kim et al. showed that a large amount of energy was needed by the planetary ball mill for grinding rice straw compared to the attrition mill.The ball milling process is generally divided into two types, the dry ball milling process, and the wet ball milling process. This article takes dry ball milling as an example to introduce the ball milling process. First, select the appropriate size and weight of the grinding medium according to the particle size of the grinding material.What is Ball Milling Process? ball mills supplier
احصل على السعر
On some problems of producing grinding media by cross
Given a high demand for steel balls for balls mills, these balls are now produced on a mass scale. In effect, manufacturers of steel balls are developing new, more and more efficient manufacturing techniques. Tomczak et al. (2013) proposed a new skew rolling process for producing balls in multiple helical impressions.The grinding process involves passing the clinker and additives through the rotating drum of the ball mill, where the grinding media crush and grind the clinker into a fine powder. The specific surface area of the resulting cement particles is carefully controlled to ensure proper setting and strength development when the cement is mixed withWhat Are the Parts of a Cement Mills? Cement Ball Mill Production Process
احصل على السعر
(PDF) DEM Investigation of Discrete Heat Transfer Behavior
This study presented a numerical model for the quantitative assessment of the heat transfer behavior of grinding media inside a ball mill. Effects of various mill speeds, grinding media fillingAnalysis of process of grinding efficiency in ball and rod mills with various feed parameters D Foszcz1, D Krawczykowski1, T Gawenda1, E Kasińska-Pilut2 and W Pawlos2 1AGH University of Science and Technology, Faculty of Mining and Geoengineering, Department of Environmental Engineering and Mineral Processing, Analiza efektywności mielenia w młynach kulowym i
احصل على السعر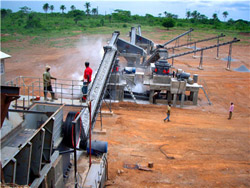
Assessing load in ball mill using instrumented grinding media
Maintaining an optimum mill load is key to improve energy utilization and hence processing efficiency. However, the grinding process is featured with opaque, unstable and highly complex flow conditions (Tang et al., 2018a), making it difficult to achieve in-situ observation of flow behavior inside a ball mill.CERAMIC LINED BALL MILL. Ball Mills can be supplied with either ceramic or rubber linings for wet or dry grinding, for continuous or batch type operation, in sizes from 15″ x 21″ to 8′ x 12′. High density ceramic linings of uniform hardness male possible thinner linings and greater and more effective grinding volume.Ball Mills 911 Metallurgist
احصل على السعر
Choosing the right strategy: cryogrinding vs. ball milling comparing
The grinding was performed in a dry state using a cryogenic grinder 6970EFM Freezer/Mill® (6970 EFM, SPEX SamplePrep, Metuchen, NJ, USA) which consisted of two stainless steel vessels, with each being able to hold four standard grinding vials. The mill was equipped with a totally enclosed liquid nitrogen (LN 2) auto-fill system, an empiric energy-model. Dry and wet grinding experiments have been carried out with a Bond mill and a laboratory stirred ball mill. During the grinding processes, the grinding time and the filling ratio have been adjusted. The second goal of this research assessed the resources, emissions andEnergy-Model and Life Cycle-Model for Grinding
احصل على السعر
Efficient preparation and characterization of graphene based on ball
The ball mill uses the kinetic energy and shear energy generated by the high-speed impact of the grinding ball to break the aluminum and thus open the fresh surface to adsorb graphite, which is more beneficial to the graphite stripping effect in the ball milling process. 2.3. Ball milling efficiency influence factor and selectionThe energy consumption of the total grinding plant can be reduced by 20–30 % for cement clinker and 30–40 % for other raw materials. The overall grinding circuit efficiency and stability are improved. The maintenance cost of the ball mill is reduced as the lifetime of grinding media and partition grates is extended. 2.5.Energy-Efficient Technologies in Cement Grinding IntechOpen
احصل على السعر
Process Control of Ball Mill Based on MPC-DO Hindawi
The grinding process of the ball mill is an essential operation in metallurgical concentration plants. Generally, the model of the process is established as a multivariable system characterized with strong coupling and time delay. In previous research, a two-input-two-output model was applied to describe the system, in which
احصل على السعر- canada gold refinery process equipment for sale
- كسارات الحجر في ولاية كارناتاكا
- جزء لكل تريليون على أسمنت أمباني
- الشركة المصنعة لمعدات كسارة الفك في تشيناي
- henan liming heavy industry
- هل يوجد مدارس تعليم معدات ثقيلة في الار
- المقاولون تعدين الفحم باليكبابان
- الرمل والحصى محطم الفلبين
- jaw crusher wearparts
- كسارة الحجر في الرمال السعودية محجر الحجر
- انخفاض سعر كسارة الفك مع شهادات ISO
- مجمع بندول الفك كسارة بايدو موسوعة
- impact crusher cap t h china
- يد حجر الجرانيت
- معالجة مناجم الحجر