اتصل
هاتف
+0086-371-86162511
عنوان
تشنغتشو ، الصين
how to design parameters for a ball mill
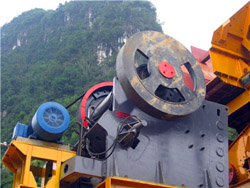
Comparative Study on Improving the Ball Mill Process Parameters
When comparing it to the factorial design, Taguchi approach delivers a more effective way to set up and arrange the process parameters. The ball mill process E.1 Determination of milling parameters in each ball size interval 100 2.1 Breakage mechanisms in a ball mill 22 2.2 First order reaction model applied to milling EFFECT OF BALL SIZE DISTRIBUTION ON MILLING
احصل على السعر
(PDF) Design of Three-chamber Ball Mill
According to the specifications and parameters of the ball mill, the general layout, grinding body, lining plate, partition device, support device, transmission part and feeding and...This work aims to design a simple horizontal ball mill. Calcium carbonate material from limestone and eggshells powder was ground using the developed ball mill. The design and optimization process of ball mill to reduce
احصل على السعر
Ball Mill Application and Design Paul O. Abbe
Ball mills are simple in design, consisting of horizontal slow rotating vessels half filled with grinding media of ¼” to 1.5”. The particles to be milled are trapped between the grinding The simulation reveals that the ball milling velocity, ball volume fraction inside the canister, ball size, and impeller shaft design are all important parameters for Modeling and Analysis of High-Energy Ball Milling Through
احصل على السعر
(PDF) Grinding in Ball Mills: Modeling and Process
A ball mill is a type of grinder widely utilized in the process of mechanochemical catalytic degradation. It consists of one or more rotating cylinders partially filled with grinding balls...In order to explore the impact of different ball milling technical parameters on the grain size of nano silicon powder, this paper adopted the orthogonal experimental design in The Impact of Ball Milling Process Parameters on the Preparation
احصل على السعر
Parameter Optimization of Ball Milling Process for Silica
The parameters used in the ball mill process are relatively large, however there are several parameters that have a significant effect on the reduction grain size Effect of operational parameters on product size and product rate was investigated. the total grinding energy consumption from 20.11 to 11.40 kW h/t by using vertical roller mill instead of AG/SAG-ball mill circuit (van Drunick et al., 2010). breakage rates of the particles are correlated with design parameters and materialOperational parameters affecting the vertical roller mill
احصل على السعر
Parameter Optimization of Ball Milling Process for Silica
The results of signal-to-noise analysis obtained the optimum parameter values in a row are: 100 rpm for milling speed parameter, 15: 1 for BPR parameter and 120 minutes for time-miling parameter. The powder size experiment verification of the ball mill process optimization parameter is D50 : 14.99 µm.A scale-up model was developed based on data of DEM simulation to quickly predict ball milling performance for different mill design and operation parameters. The ball milling performance was characterized by grinding rate and power draw. The damping energy of ground particles obtained from DEM simulation was used to A DEM based scale-up model for tumbling ball mills
احصل على السعر
Ball Mill an overview ScienceDirect Topics
Quantum Nanostructures (QDs): An Overview. D. Sumanth Kumar, H.M. Mahesh, in Synthesis of Inorganic Nanomaterials, 2018 3.6.1.1 Ball Milling. A ball mill is a type of grinder used to grind and blend bulk material into QDs/nanosize using different sized balls. The working principle is simple; impact and attrition size reduction take place as the ball The contact parameters used in the present work were estimated following a procedure detailed elsewhere (Rodriguez, 2016).This set of parameters was used by Rodriguez et al. (2018) to investigate mixing in ball mills and, more recently, on predicting the Bond ball mill work index using the UFRJ mechanistic mill model (Rodriguez et al., Mechanistic modeling and simulation of a batch vertical stirred mill
احصل على السعر
EFFECT OF BALL SIZE DISTRIBUTION ON MILLING
E.1 Determination of milling parameters in each ball size interval 100 2.1 Breakage mechanisms in a ball mill 22 2.2 First order reaction model applied to milling 24 2.3 Grinding rate versus particle size for a given ball diameter 25 2.4 Cumulative breakage function versus relative size 28 3.3 Experimental design 47 3.4 Mono-sized mediaThe new insight obtained into the ball mill grinding operation can help develop improved approaches to the design and scale-up of ball mills. After determining the model parameters, the mill(PDF) Effects of Ball Size Distribution and Mill Speed and
احصل على السعر
Modeling and Analysis of High-Energy Ball Milling Through
The effects of major processing parameters of attritor mills on ball milling efficiency (i.e., minimum energy consumption with maximum milling progress) are investigated using discrete element modeling (DEM). The major processing parameters investigated include the size of balls, ball volume fraction inside the canister, ball milling Planetary ball mill is a powerful tool, which has been used for milling various materials for size reduction. The discrete element method (DEM) was used to simulate the dynamics of particle(PDF) Simulation of a Laboratory Scale Ball Mill via
احصل على السعر
Analiza efektywności mielenia w młynach kulowym i
mm were replaced with 80 mm balls to reduce the amount of coarser particles in circulation. Larger balls reduced the number of particles coarser than 1 mm by about 5%. In case the feed to ball mill was equal to 1200 Mg/h, it resulted in a reduction of 60 Mg/h of the weight of coarse particles in circulation. It also enabled the processing of aRod Mill Design Calculations. EF1 Dry Grinding for the same range of work, dry grinding requires 1.3 times as much power as wet grinding. EF2 Open Circuit Grinding when grinding in open circuit ball Rod Mill Design Calculations 911 Metallurgist
احصل على السعر
Modelling the performance of industrial ball mills using
(b) For the 4.0 m and 4.5 m diameter mills, the cyclone underflow percent solids and the cyclone operating pressure are low; these circuits can be optim- ized by changing the cyclone design parameters. The number of mills of a given diameter required to achieve a capacity of 10,000 tonnes/day can be selected from these simulation results.In order to explore the impact of different ball milling technical parameters on the grain size of nano silicon powder, this paper adopted the orthogonal experimental design in combination with fitting analysis, and set the agitator shaft speed of the ball mill and the milling time as the influence factors. Then this paper studied the impact ofThe Impact of Ball Milling Process Parameters on the Preparation
احصل على السعر
Parametric study on four station ball mill for synthesis of
The objectives of a parametric study on a four-station ball mill for the synthesis of ultrafine powders include: •. Optimization of milling parameters, such as milling time, ball size, ball-to-powder ratio, rotational speed, and type of milling media, to achieve the desired properties of the synthesized powders. •.V — Effective volume of ball mill, m3; G2 — Material less than 0.074mm in product accounts for the percentage of total material, %; G1 — Material less than 0.074mm in ore feeding accounts for 0.074mm in the percentage of the total material, %; q’m — Unit productivity calculated according to the new generation grade (0.074mm), t/(m3.h). The Ball Mill Parameter Selection & Calculation JXSC
احصل على السعر
A Review of Advanced Ball Mill Modelling J-STAGE
A major advance in the modeling of ball mills became possible through the development of the discrete element method. DEM provides a numerical procedure for solving Newton’s second law with an appropriate contact relationship that can be applied to describe the motion of each grinding medium contained in the mill charge to predict element position, Ball Mill Design Parameters. Size rated as diameter x length. Feed System. One hopper feed; Diameter 40 100 cm at 30 ° to 60 ° Top of feed hopper at least 1.5 meter above the center line of the mill.AMIT 135: Lesson 7 Ball Mills & Circuits Mining Mill
احصل على السعر
Variables in Ball Mill Operation Paul O. Abbe®
A Slice Mill is the same diameter as the production mill but shorter in length. Request Price Quote. Click to request a ball mill quote online or call 630-350-3012 to speak with an expert at Paul O. Abbe® to help you determine which design and size ball mill would be best for your process. See our Size Reduction Options.Analysis of Variant Ball Mill Drive Systems. The basic element of a ball mill is the drum, in which the milling process takes place ( Figure 1 ). The length of the drum in the analyzed mill (without the lining) is 3.6 m, and the internal diameter is 3.4 m. The mass of the drum without the grinding media is 84 Mg.Energy Efficiency Analysis of Copper Ore Ball Mill Drive
احصل على السعر
Performance optimization of an industrial ball mill for
The energy consumption in the ball mill was found to be 6.5 kWh/t of ore with a targeted product size below 1 mm. The BWI of the ores varied from 5.8 to 7.8 kWh/t to reduce the particle size below 100 μ m, but in real time, the energy consumption is very high compared with the reported value of 6.5 kWh/t.
احصل على السعر- مصانع التعدين المحمولة مطحنة الكرة
- المنقولة كسارة الخرسانة المتنقلة للبيع شيكاغو مطحنة الكرة
- processing gold ore step by ste
- تركيز معالجة خام أكسيد النحاس
- معدات المحاجر البلوك
- الحجر الطاحن المغناطيسي
- buy mining machinery mining13
- تبين لي حساب قدرة الكرة مطحنة في
- محجرة كوسيدير في البوير
- الهيدروليكية كسارة خرسانة الصين
- Bzmachine Crusher Crushing System
- الاقتصادية المجوهرات المتداول المطاحن
- کارخانه سنگ معدن طلا
- الهيماتيت محطة الرسم البياني كسارة خام الحديد
- impact crushers stedman