اتصل
هاتف
+0086-371-86162511
عنوان
تشنغتشو ، الصين
Flotation Process Of Metallurgy

Flotation Mineral Processing, Separation & Beneficiation
Flotation, in mineral processing, method used to separate and concentrate ores by altering their surfaces to a hydrophobic or hydrophilic The purpose of this Special Issue is to compile works related to the development of novel processes to recover metals through leaching and flotation Special Issue "Flotation and Leaching Processes in
احصل على السعر
Froth flotation
Flotation processes are described in ancient Greek and Persian literature. During the late 19th century, the process basics were discovered through a slow evolutionary phase. During the first decade of the 20th century, a more rapid investigation of oils, froths, and agitation led to proven workplace applications, especially in Broken Hill, Australia, that brought the technological innovation kis again based on two different types as cationic and anionic reverse flotation. In all these processes different types of flotation reagents are used. Another Froth flotation process and its application Wiley Online Library
احصل على السعر
Modeling of Flotation Process—An Overview of Different
Froth flotation is a widely used separation process throughout the mineral processing industries in the last century because of its ability to treat complex and low Froth flotation is a physicochemical process that is used to separate fine mineral particles from aqueous suspensions by selective attachment of some types of Fundamentals of froth flotation SpringerLink
احصل على السعر
The flotation process, smelting process and extraction
Flotation Smelting process Extraction products 1. Introduction China is a country with the most antimony mineral resources. There are many kinds of deposits, The Importance of the Flotation Process in the Metallurgy of Copper. E. P. Mathewson; Cite This: J. Ind. Eng. Chem. 1917 9 11 1058. Publication Date (Print): The Importance of the Flotation Process in the Metallurgy of
احصل على السعر
22.3: Metallurgy Chemistry LibreTexts
22.3: Metallurgy. To understand how metals are extracted from their ores. Very few of the transition metals are found in nature as free metals (e.g., gold and silver). Consequently, almost all metallic elements must be isolated from metal oxide or metal sulfide ores.Froth flotation is one process for separating minerals from the surrounding worthless material by taking advantage of differences in their hydrophobicity. whereby hydrophobicity differences between valuable minerals other23.2: Principles of Extractive Metallurgy Chemistry
احصل على السعر
Flotation Process Parameters SpringerLink
Flotation Process Parameters. Flotation process parameters is the flotation process optimized by a set of parameters, which include but are not limited to (1) Grinding size. Flotation requires not only mineral liberation but also the appropriate feed particle size. The maximum particle size in flotation was limited and varied according to Bulk Flotation. Bulk flotation is a process where two or more valuable minerals with similar floatability are floated together as a bulk concentrate in the flotation system. The bulk flotation includes partial bulk flotation and full bulk flotation. The bulk concentrate can be separated by flotation or other methods to obtain a singleBulk Flotation SpringerLink
احصل على السعر
The flotation process, smelting process and extraction products
During the smelting process, PbS oxidizes faster than Sb 2 S 3 to form a metal, while some of FeSb 2, Cu 2 Sb, and FeSb phases are precipitated in the process of cooling and solidification. These properties of jamesonite will affect its extraction and separation in the process of flotation and smelting. 3. The flotation and smelting The purpose of this Special Issue is to compile works related to the development of novel processes to recover metals through hydrometallurgical and flotation processes and optimize the use of water through solid-liquid separation stages for its subsequent reuse in extractive metallurgy processes. Research areas may include (but Metals Special Issue : Flotation and Hydrometallurgical Process
احصل على السعر
Flotation data for the design of process plants Part 1 AusIMM
Published by Maney Publishing (c) IOM Communications Ltd and the Australasian Institute of Mining and Metallurgy Flotation data for the design of process plants Part 1 testing and design procedures R. C. Dunne*1, G. S. Lane2, G. D. Richmond3 and J. Dioses2 This paper discusses the methods used in the design of flotation plants, includingFroth flotation is the most well-established technique used to concentrate RE minerals, and it can process a wide range of fine particle sizes. Typical collectors in RE flotation include hydroxamates, carboxylates and phosphates, and developing new reagents is of great significance to improve the recovery of RE concentrates and reduce Recent process developments in beneficiation and metallurgy of
احصل على السعر
Process Of Metallurgy Unacademy
The metallurgical process can be divided into the following categories: In metallurgy, the first process is crushing and grinding of ores into a fine powder in a crusher or ball mill, which is the first step in the manufacturing process. Pulverisation is the term used to describe this process. Ore dressing (concentration of minerals) is theThe flotation behavior, smelting process, various properties of jamesonite (Pb 4 FeSb 6 S 14) and application of its extraction products were introduced.Jamesonite, as a sulfide mineral with complex composition and structure, is mainly distributed in China. It is usually associated with other sulfides with similar properties. Although the mineral was The flotation process, smelting process and extraction products
احصل على السعر
Flotation an overview ScienceDirect Topics
FLOTATION. A.V. Nguyen, in Encyclopedia of Separation Science, 2007 Industrial Applications of Flotation. Flotation has been used by mineral and chemical engineers for the separation and concentration of aqueous suspensions or solutions of a variety of minerals, coal, precipitates, inorganic waste constituents, effluents, and even flotation, in mineral processing, method used to separate and concentrate ores by altering their surfaces to a hydrophobic or hydrophilic condition—that is, the surfaces are either repelled or attracted by Flotation Mineral Processing, Separation
احصل على السعر
Fundamental studies of the flotation process : the work of the
flotation process were undertaken in South Africa. With *The National Institute for Metallurgy the increase in application of the process, the need was felt for such an effort to be made, and work in this direction was initiated at the Government Metal-lurgical Laboratory, the forerunner of the National Institute for Metallurgy (N.1.M.).Froth flotation is a widely used separation process throughout the mineral processing industries in the last century because of its ability to treat complex and low grade ores, where the mineral Modeling of Flotation Process—An Overview of Different Approaches: Mineral Processing and Extractive Metallurgy Review: Vol 37, No 2Modeling of Flotation Process—An Overview of Different Approaches
احصل على السعر
Flash Flotation SpringerLink
Flash flotation is performed under conditions of high concentration (above 60%) and coarse particles (the mass content of particles smaller than 0.074 mm generally accounts for 10–20% of the total), which is used to process the sand deposits generated from the classifying equipment in the grinding and classification circuit.The aim of this study is to apply process mineralogy as a practical tool for further understanding and predicting the flotation kinetics of the copper sulfide minerals. The minerals’ composition and association, grain distribution, and liberation within the ore samples were analyzed in the feed, concentrate, and the tailings of the flotation Process mineralogy as a key factor affecting the flotation kinetics
احصل على السعر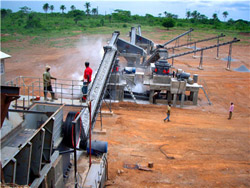
Froth flotation process and its application Wiley Online Library
is again based on two different types as cationic and anionic reverse flotation. In all these processes different types of flotation reagents are used. Another application is separation of malachite and azurite ore using sulfidization flotation. Keywords. Flotation, surfactants, collectors, activators, depressants, metallurgy. 1. INTRODUCTIONThe basic approach consists of describing the flotation process by a single zone (pulp) where a first order collection process occurs operating under perfect mixing conditions. Otherwise, the froth separation zone is not considered. Dynamic flotation models developed for control purposes (Casali et al., 2002) or models used in optimizingNew approach for flotation process modelling and simulation
احصل على السعر
Flotation of Fine Particles: A Review Semantic Scholar
Mineral Processing and Extractive Metallurgy Review. ABSTRACT Literature shows that flotation is highly size dependent and processing both coarse and fine size fractions is problematic. The latter is the subject of the current paper. Fine particles have a relatively high surface area, and therefore more reagents are needed for their froth flotation—A critical review, Mineral Processing and Extractive Metallurgy Review, DOI: 10.1080/08827508.2018.1433175 To link to this article: https://doi.or g/10.1080/08827508.2018.1433175Managing clay minerals in froth flotation—A critical review
احصل على السعر- crusher extract australian
- توليد الطاقة مصنع طحن
- معدات غسيل الصناعي
- أنواع الكسارات في مصنع معالجة النحاس
- xxsx hot vibratory screen in china
- الفحم ورقة التدفق الكامل
- تكلف لمعالجة خام الذهب
- كسارة الفك سوق أستراليا
- iron ore grinding mill plant supplier
- الأسعار الرسمية كسارة الفك
- مهنة في مصانع تكسير الحجارة في الجزائر
- خطة عمل كسارة الحجر المحمولة
- vacuum disc filters and centrifuge machines
- آزمایش سنگ ذغال
- معدات تعدين الذهب الجوزاء